IT Support for Manufacturers: Recommendations for manufacturers
by Jon Lober | NOC Technology
We get it: Manufacturers have unique IT needs.
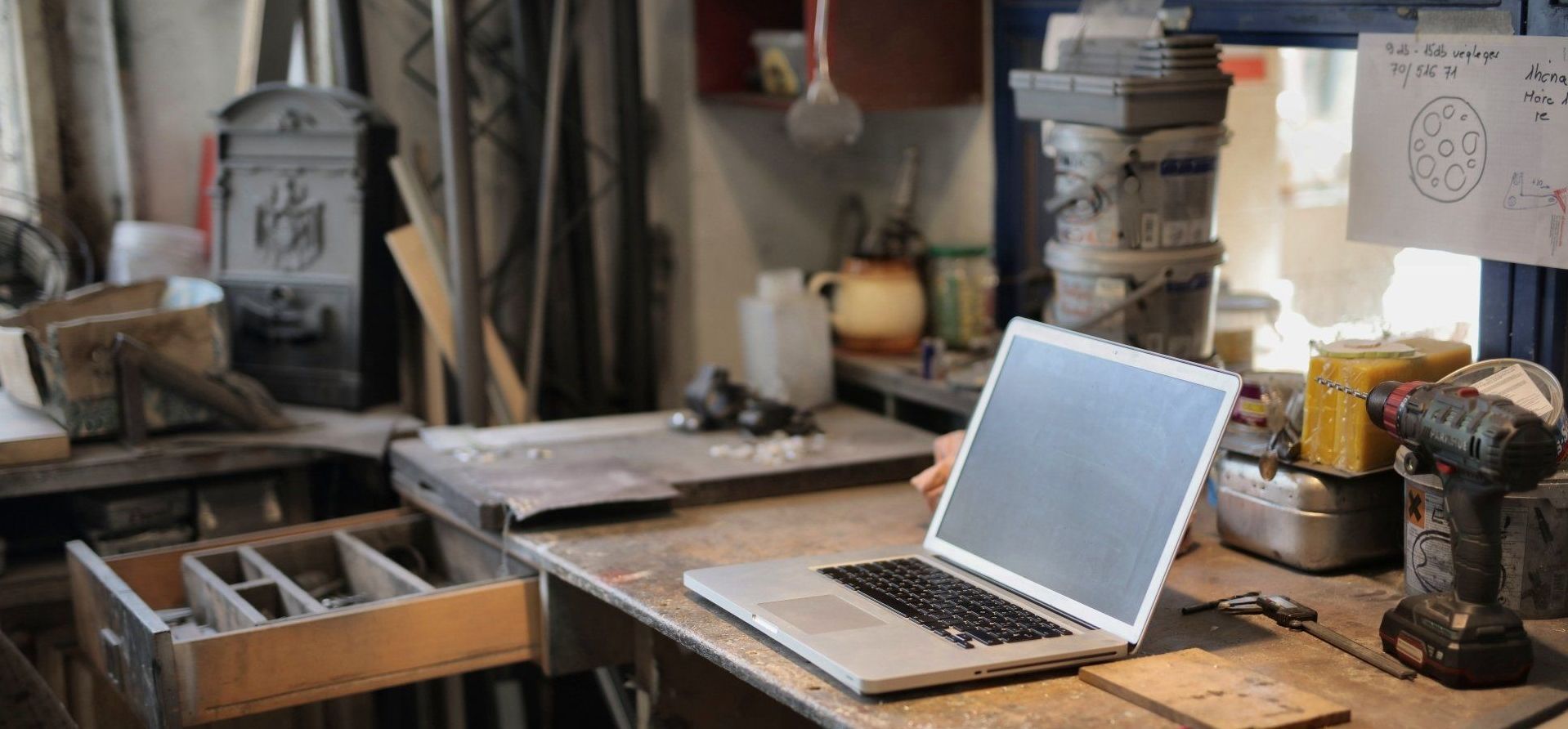
Though every business should leverage IT for administrative and customer-service roles, manufacturers also rely on IT to manage their critical operations: from production processes to tracking inventory to order fulfillment.
Despite its significance to their business’s existence, many manufacturing companies continue to operate with limited (or nonexistent) expert support, which can have significant consequences on overall efficiency, security, and competitiveness.
Reasons a US manufacturer should consider outsourcing their IT support
- High cost of downtime. Inefficient computers, network failures, or buggy software are a hassle in any industry, but in the breakneck world of manufacturing deadlines, downtime can quickly sink a struggling company. Just how much does downtime cost you? Check it out using our downtime calculator.
- High risk of ransomware attack. Because they know you can't afford downtime, cybercriminals are targeting manufacturers with ransomware designed to hold your production hostage until their demands are met.
- Complexity of interfacing the digital and physical world. Manufacturing technology must often interface directly with IT systems—creating an unusual bond between the digital and physical world. This relationship can be quite sensitive to changing parameters and vulnerable to unique types of cyberattacks that can compromise the quality and integrity of a manufacturer’s product.
- Access to qualified labor. Manufacturers often struggle to employ and maintain a high-quality administrative and manufacturing workforce. The burden of attracting and retaining capable technical talent in an often low tech-trained environment adds another challenge for recruiters and HR.
- Compliance. Whether it’s OSHA, NIST, CMMC, or ISO, the constantly-changing expectations for privacy, security, safety, and quality compliance can quickly overwhelm a manufacturer trying to stay in bounds and maintain large government contracts.
What to prioritize in an IT partner
Although outsourced IT support cannot solve all of a manufacturer’s problems, a competent managed service provider (MSP)—or better yet, complete outsourced IT department—can unload a significant burden from your management team. A quality MSP can provide as much or as little support as a manufacturer needs through fully-managed or co-managed IT arrangements. Here's what our experts think you need to prioritize in a partner:
- Industry experience. The crucial role of tech in manufacturing means that the system is either running smoothly or disrupting everyone. A manufacturer’s IT provider should have significant and demonstrable experience in manufacturing. Period. You should ask for industry references and check them out before moving forward.
- Compliance support. Since manufacturers are already dealing with a pile of changing regulations, they should prioritize an IT partner that can manage emerging national and state regulations that dictate compliance for privacy, data management, and cybersecurity concerns. Currently we're navigating the rollout of CMMC, so you'll want to find a provider who is competent and comfortable with the ins and outs of CMMC.
- Cybersecurity expertise. Manufacturers must prioritize an MSP that provides multilayered cybersecurity model that includes employee training, anti-phishing measures, proactive ransomware monitoring, and access to cyber insurance.
- Scalability. If a manufacturer goes through a period of intense growth, they do not want to be held back by an outside service provider. Since market demand can fluctuate widely for many products, manufacturers should identify MSPs that have the technical ability and staffing capacity necessary to grow with them as quickly as needed.
- Downtime prevention. A quality MSP should be able to limit downtime to an absolute minimum through careful and strategic monitoring and maintenance. Manufacturers should prioritize MSPs that have a proven track record in providing maximum uptime through private servers, cloud servers, or a hybrid model.
NOC takes care of us. We had a license managing server for our SolidWorks program that our engineers use daily, go down. NOC realized it was down, called us, and had a tech in route before we ever knew it was down.
Doug Holdmeyer,
Schwoeppe Machine & Tool
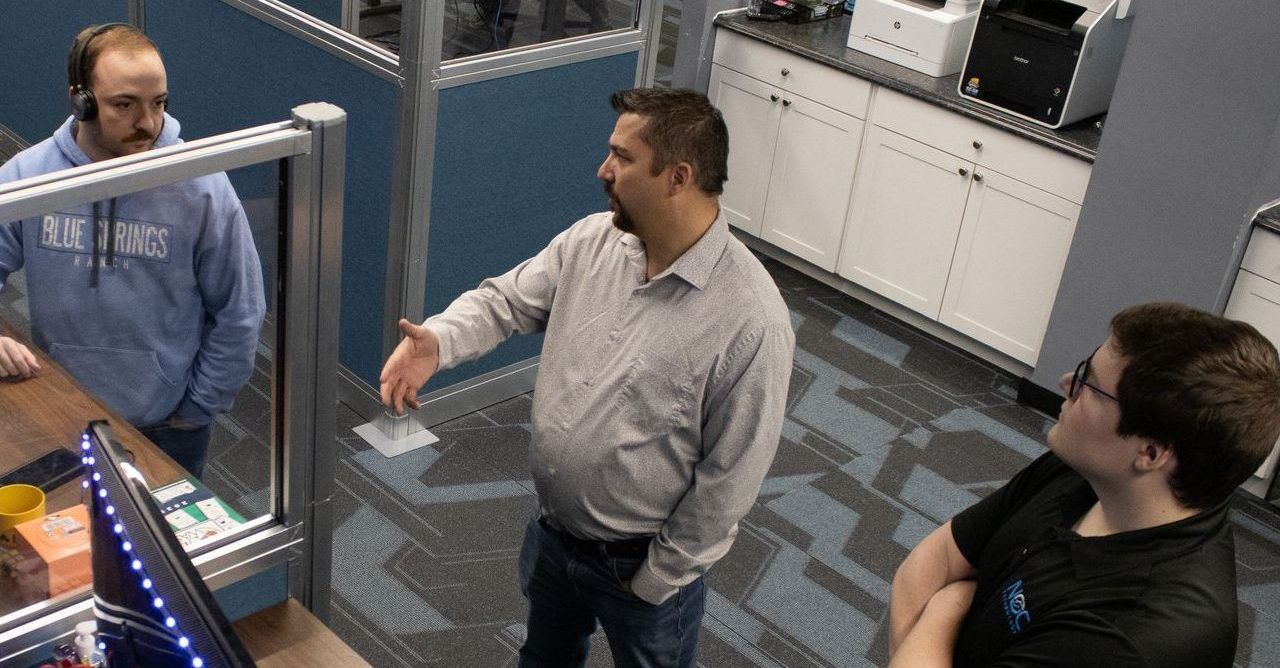
Our approach: Simplified IT for complex operations.
We keep you compliant. Whether it's NIST or a version of ISO, we understand the compliance software requirements behind US manufacturing.
We keep you running. Downtime is expensive. We limit downtime by proactively monitoring and maintaining your network.
We keep you prepared.
Through business continuity & disaster recovery planning, we help you prepare for any unforeseen event.